Case Studies
Case Examples
High-precision weighing for auxiliary raw materials shortened from "40h" to "8h"!
Weighing Process
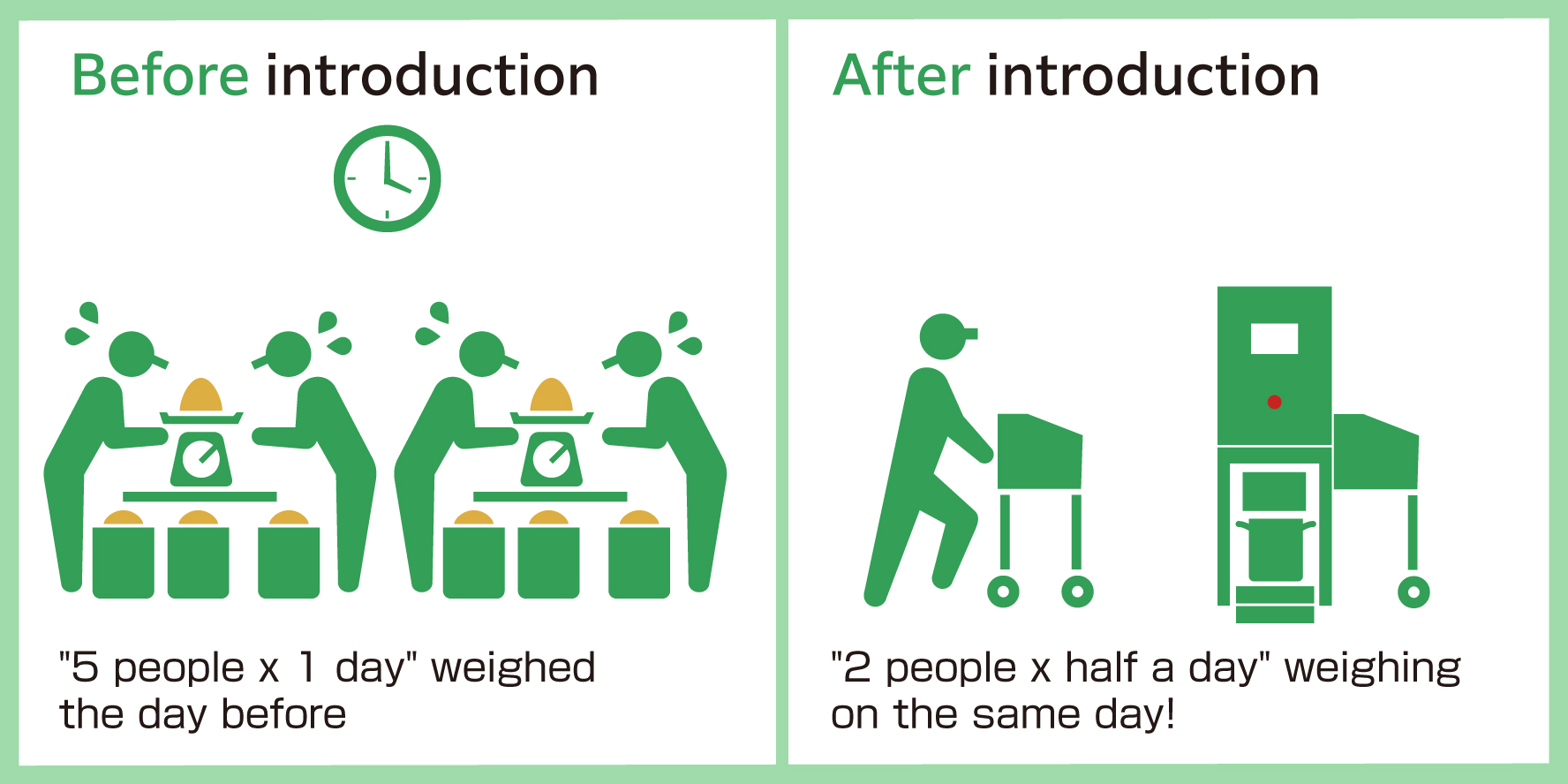
Type of Industry
Confectionery manufacturer
Introduced Products
Divider Scale Terminal Detachable System
Background and problem
Increase the burden of weighing work corresponding to high-mix, low-volume production
At a confectionery factory, main ingredients such as rice flour and mochi flour were weighed automatically, but auxiliary ingredients such as granulated sugar and lactic acid bacteria were weighed manually. The idea was that a large variety of auxiliary raw materials should be made by hand, but with the progress of high-mix, low-volume production, the strictness required for weighing work increased, and finally, it took five full-time staff to complete the entire day. Due to the labor shortage in recent years, it was difficult to transfer workers from other processes, which was a major concern.
◎ The challenges of manual high-precision weighing
● Staffing needs to be proportional to the amount of work
● Operator familiarity is required
● Time and effort to adjust for minor of errors
● Paying close attention to dust scattering
● Operator familiarity is required
● Time and effort to adjust for minor of errors
● Paying close attention to dust scattering
Suggestions from TSUKASA
Greatly improve efficiency with stocker detachable weighing machine
We have suggested a "Divider Scale Terminal Detachable System" that can be used at up to four locations where raw material stockers can be attached and detached, and that can be mixed by replacing the added raw materials. Eight stockers were prepared to be used in rotation.
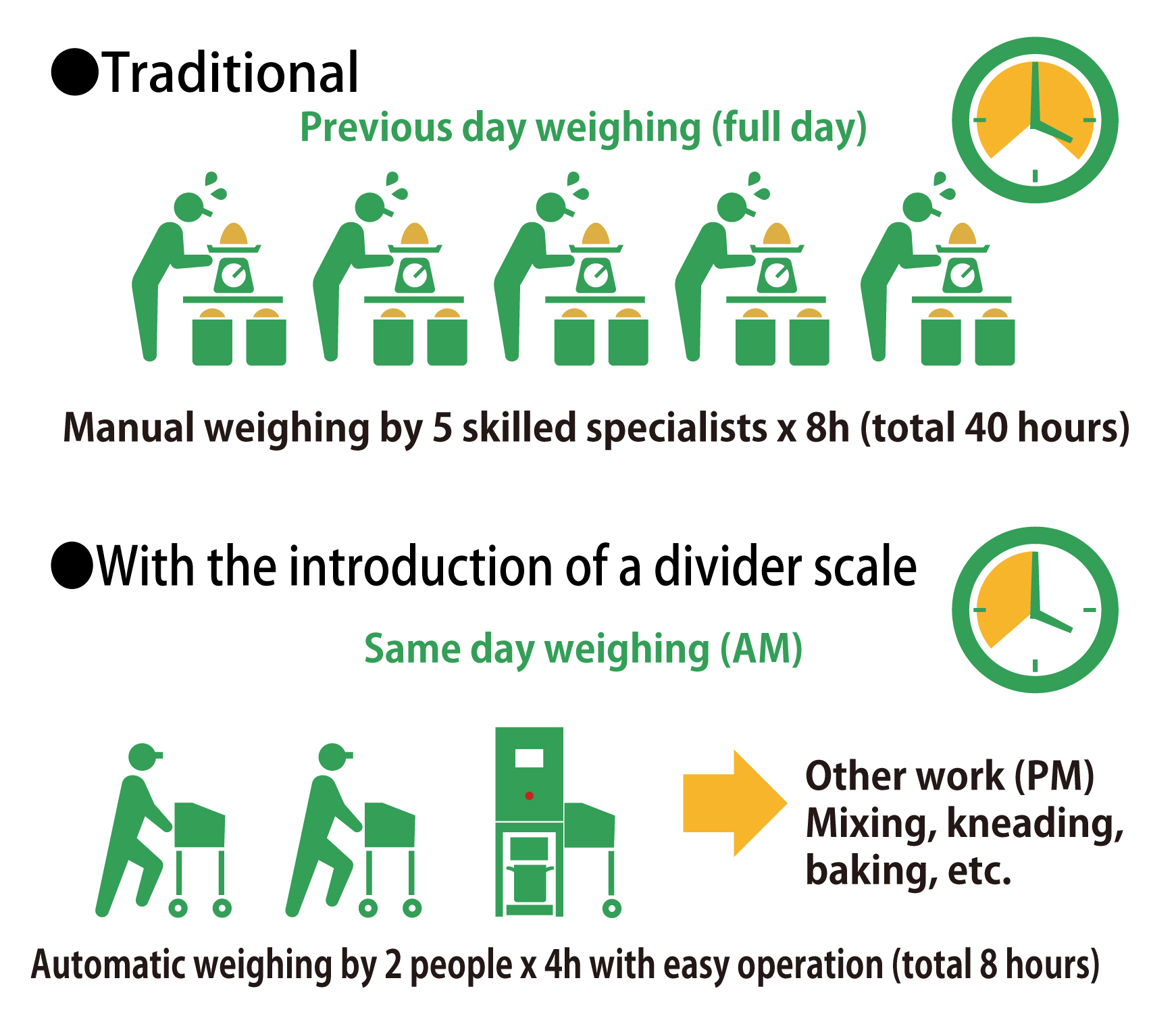
Previous day weighing
"5 people x 8 hours" for full day (total 40 hours) shortens to
↓
Same day weighing
"2 people x 4 hours" (total 8 hours)!
"5 people x 8 hours" for full day (total 40 hours) shortens to
↓
Same day weighing
"2 people x 4 hours" (total 8 hours)!
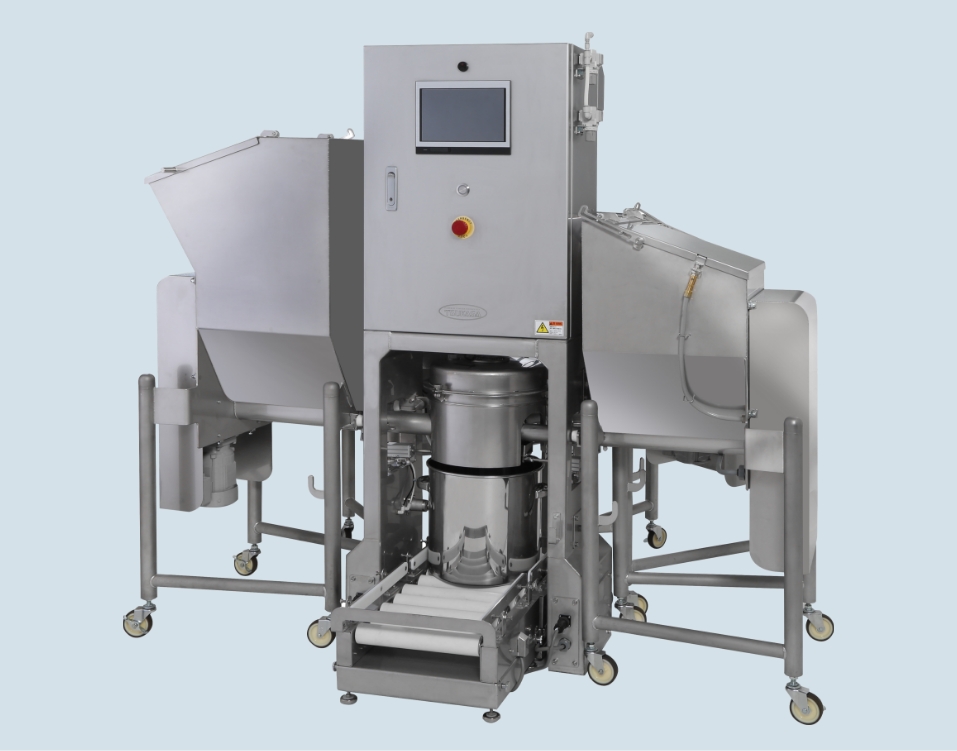
Divider Scale Terminal Detachable System
Results of introduction
A lot of room for staffing
Significant efficiency improvements reduce the number of people involved in weighing work, and more people can be transferred to other processes. There are no more cases where managers are forced to enter the production line due to labor shortages.
Elimination of weighing errors and "selection errors"
Since it is automatic weighing, there is no worry of human error. There are no longer errors caused by operators selecting from materials that look similar, and weighing the wrong ones.
Contributes to recruitment and retention rates
Reducing the burden on the workers also contributes to solving the problem of people immediately resigning. In addition, consideration for the working environment can be expected to be a strength even for new hires.
Contributes to labor saving and is economical
It is possible to mix and weigh multiple raw materials in the same container and bring them into the next process as they are. Additionally, there is no need to measure each raw material in a bag, which is economical because it reduces the number of bags used.