Case Studies
Case Examples
Updating Plant Facility Programs with Remote Tools
Services
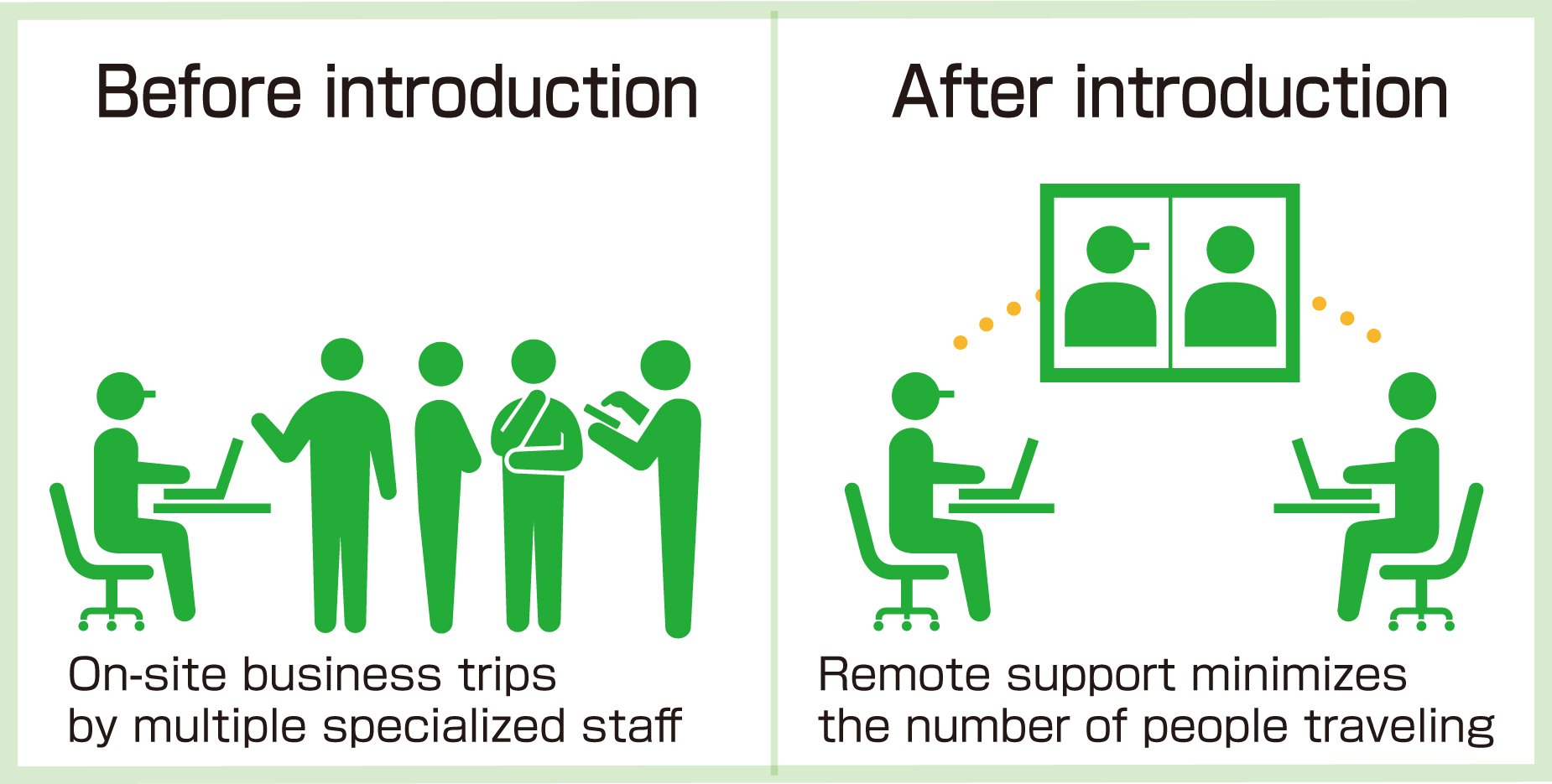
Type of Industry
Food manufacturers (e.g. overseas plants)
Introduced Products
Remote desktop tools, etc.
Customer requests
Starting up new equipment with a minimal number of people traveling
TSUKASA received inquiries from overseas customers stating that: "We want to speedily start up new plant facilities at a low-cost," and "We also want to change the line and update the program of existing facilities.” Traditionally, multiple specialized staff for electrical facilities, machinery, and installation visited the customer's site to set up the sequencer, which is the "key to control.”
Suggestions from TSUKASA
Check the control of the sequencer using remote tools
Using remote tools, we obtained permission to access PCs at customers' overseas plants from TSUKASA's head office and remotely sent programs and checked and modified the sequencer control.
The work procedure is simple
(1) Connect a PC to the Internet at the plant and start up a remote tool.
(2) Connect the PC to the sequencer in the plant facility.
(3) Connect the PC to TSUKASA's PC.
(4) Check and modify the sequencer control from TSUKASA's PC.
All you have to do is set up a PC and the Internet!
Of course it's also possible to carry out remote operation from the customer's head office or sales base.
(2) Connect the PC to the sequencer in the plant facility.
(3) Connect the PC to TSUKASA's PC.
(4) Check and modify the sequencer control from TSUKASA's PC.
All you have to do is set up a PC and the Internet!
Of course it's also possible to carry out remote operation from the customer's head office or sales base.
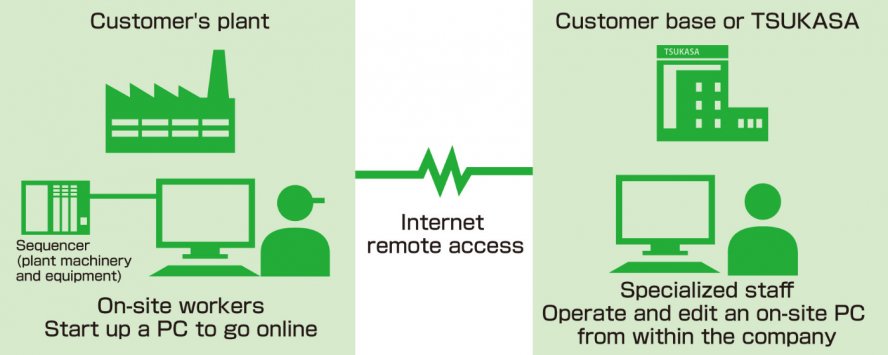
Results of introduction
Minimizing the number of people traveling
This was at a time when COVID-19 was already spreading, and we were able to minimize the number of people entering customers' plants from the outside.
Speedy response by using remote operation
We were able to save on the schedule adjustments and travel time for business trips by multiple people, and achieved a speedy response overall.
Great cost advantages
We were able to reduce the overall cost because the remote operation does not require a large amount of travel expenses.
Work quality is firmly maintained
Since the remote operation was performed by skilled specialized staff from TSUKASA, we were able to maintain the same quality of work as our on-site support.