Case Studies
Case Examples
Stabilizing Quality by Crushing Lumps of Confectionery Materials
Crushing and Milling Process
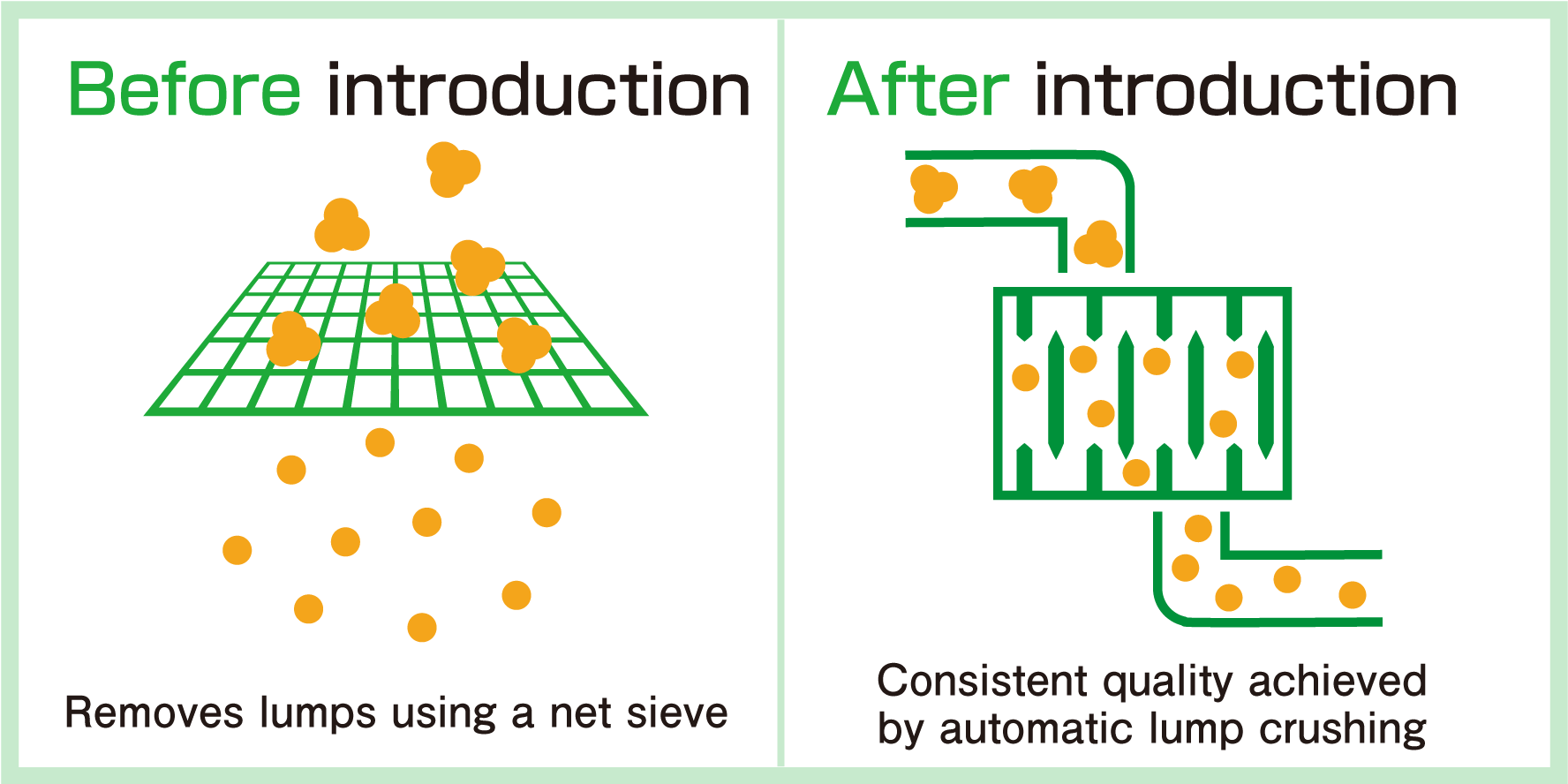
Type of Industry
Confectionery manufacturer (chocolate factory)
Introduced Products
PowCrusher
Background and problem
We would like to eliminate the lumps in cacao mass when it is placed into a mixer
At a chocolate factory, a plan to fully automate the line by pneumatic conveyance was underway. One issue was that lumps of cacao mass, which is rich in oil, were easily formed during conveyance. As a result, the quality of the cacao mass became inconsistent when mixed with sugar and milk.
The customer of the factory consulted with us, stating "We are currently carrying out sifting over a net to get rid of lumps and prolong the mixing time to obtain a consistent quality. Do you have any solutions in terms of streamlining this operation?"
The customer of the factory consulted with us, stating "We are currently carrying out sifting over a net to get rid of lumps and prolong the mixing time to obtain a consistent quality. Do you have any solutions in terms of streamlining this operation?"
Suggestions from Tsukasa
Automatic crushing through the incorporation of a PowCrusher into the line
We investigated a method using a PowCrusher. Before the ingredient was put into a mixer, any lumps were crushed with the equipment's internal rotating and fixed blades. Using a sample of cacao mass provided by the customer, we repeated crushing tests to ensure consistent quality before deciding to use this method.
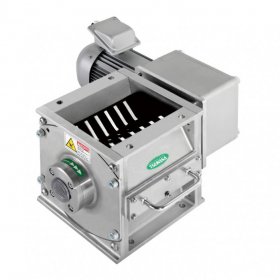
Why TSUKASA was chosen
Small size makes it easy to be integrated into a line
The best feature of TSUKASA's PowCrusher is its compact size—it is smaller than those of other manufacturers, making it easier to integrate into the design of lines. It can also be easily added to existing lines.
Results of introduction
Reduction of waste through consistent quality
Compared to manual lump removal, the quality has become consistent, and waste was significantly reduced which served as a cost-saving measure.
Prevention of contamination by foreign substances
Since there is no human involvement between the tank and mixer, and all work was done in-line, and prevention of foreign substances getting contaminated was realized.
Reduction of the number of operators across the line
The number of operators was reduced line-wide, contributing to solving a labor shortage issue in the manufacturing site.