Case Studies
Case Examples
Stabilizes continuous automatic powder feeding at noodle factories
Material Receiving and Powder Feeding Process
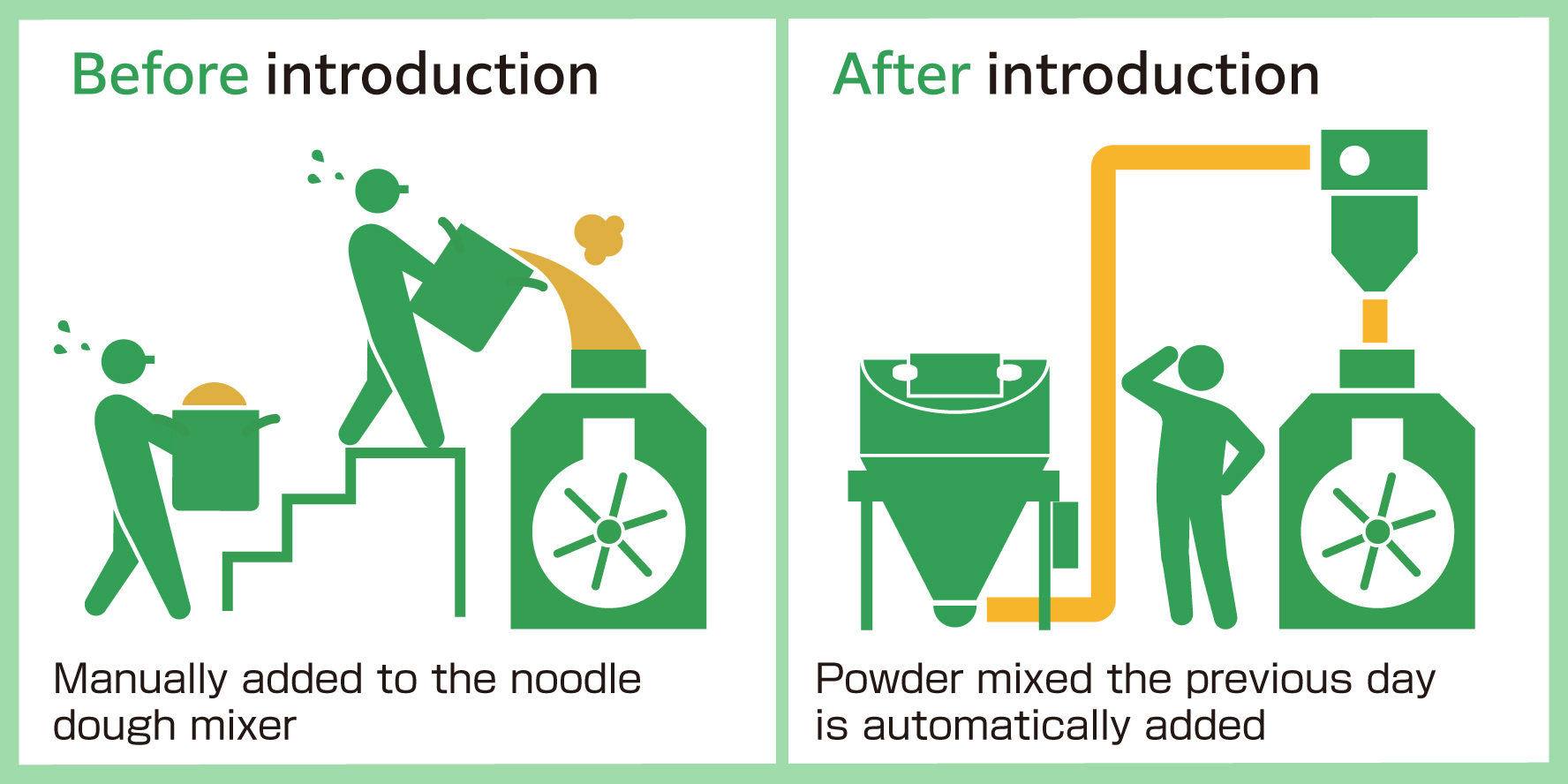
Type of Industry
Noodle manufacturer
Introduced Products
Automatic bag opening System, etc.
Customer requests
High-efficiency operation of the line to support a wide variety of products
In a noodle-making factory that continuously runs the noodle belt through the line (without cutting the belt), strict time management is required even in the supply of powder raw materials. One customer asked us to increase the productivity of the entire line by supplying flour to the noodle dough mixer at just the right time to support multi-product production.
In this customer's factory
● Various types of raw materials are used
● A wide variety of noodle products are also available
● There are a high number of batches per day
● A wide variety of noodle products are also available
● There are a high number of batches per day
Suggestions from TSUKASA
Introduced mixing the previous day, and making noodles on the day
We proposed a system in which flour and additives can be mixed the day before and put into the noodle dough mixer immediately the next day.
Work on the previous day
Powder raw materials for the next day are mixed and stored in a silo
Work on the day
The required amount for each batch is automatically added to the noodle dough mixer
↓
With the noodle dough mixer, all you have to do is add water to the mixed powder ingredients and knead them!
↓
With the noodle dough mixer, all you have to do is add water to the mixed powder ingredients and knead them!
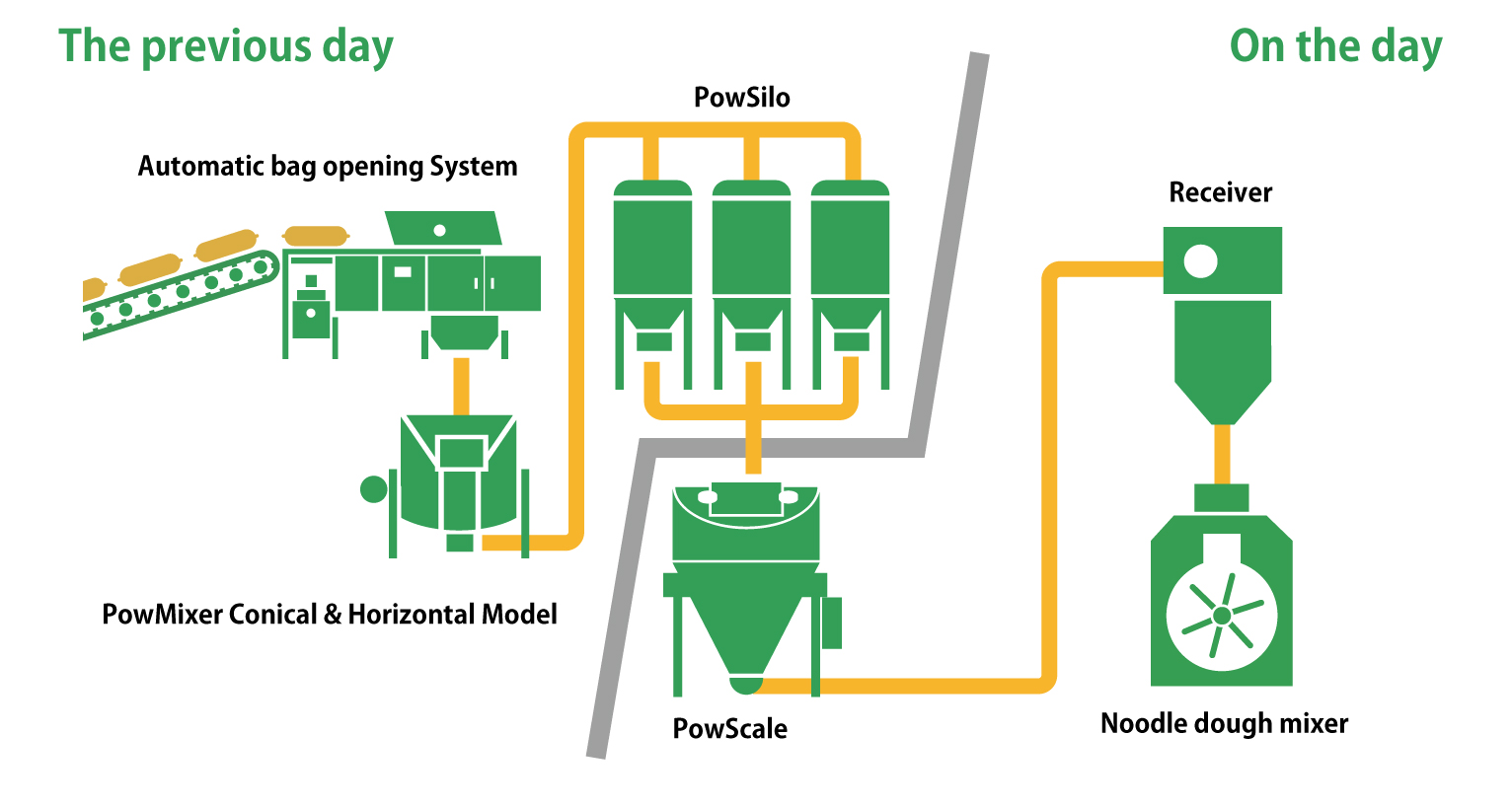
No powder residue when changing raw materials
A hopper type is adopted for the discharge part of the Automatic bag opening System so that there is no powder residue when switching powder raw materials to be used. It is possible to discharge the entire amount by falling under its own weight.
Manual supply of raw material bags
In order to supply a wide variety of raw materials in a high frequency and timely manner, raw materials to the automatic bag opening machine are supplied manually (inclined conveyors) instead of automatically. We have made it possible to respond flexibly while observing the status of the line.
Results of introduction
Shorten the mixing time of the noodle dough mixer
Since multiple powder ingredients can be mixed and supplied to the noodle dough mixer, kneading time is greatly reduced compared to adding a mixer for each type of powder. High-efficiency operation of the mixer was achieved.
Instant feeding to the noodle dough mixer
Remove the mixed powder ingredients from the silo, weigh one batch, and move it to the receiver at the top of the noodle dough mixer. As the noodle dough was discharged from the mixer, the next ingredient was dropped at the same time, so loss time was eliminated.
Reduce the burden on workers who are pressed for time
Compared to "manually adding powdered ingredients while watching the situation of the noodle dough mixer," the burden on workers who are pressed for time is greatly reduced. The anxiety of not being able to make the next batch in time because of something going wrong was eliminated.