Case Studies
Case Examples
Aiming for zero defect rate by supplying bags to bag-opening equipment
Material Receiving and Powder Feeding Process
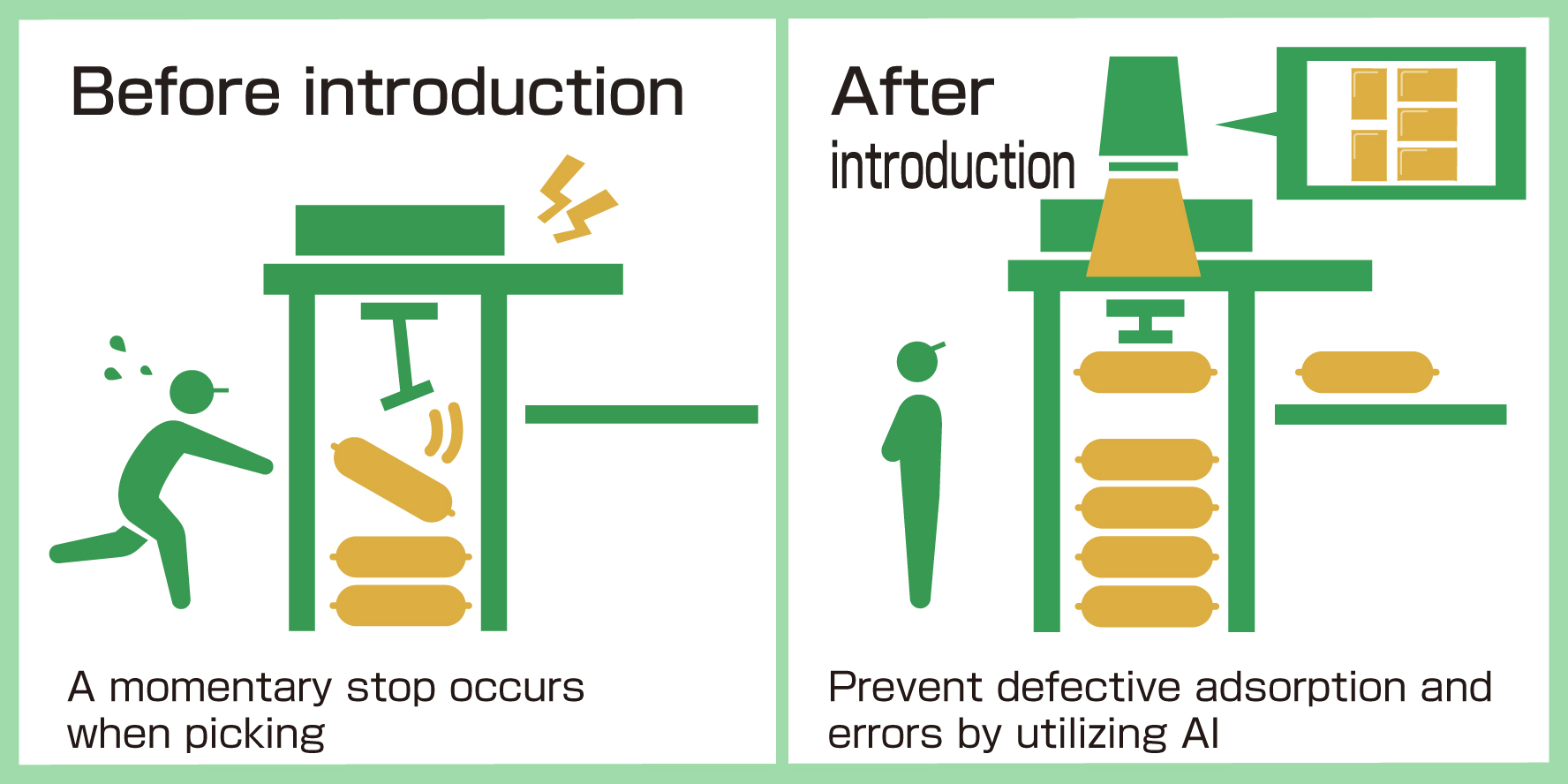
Type of Industry
Confectionery manufacturer
Introduced Products
Depalletizer Robo PV (PowVision)
Background and problem
Raw material bags varied due to an increase in imported raw materials
When picking palletized raw material bags and feeding them to the "automatic bag-opening system," a momentary stop often occurred. In particular, imported raw material bags are often piled up in a cluttered manner as a result of long shipping and land routes, as well as varied shapes of the bags. A momentary stop was caused mainly by a picking error when the bag was loaded onto a "Depalletizer Robo," an automatic conveyor machine. Therefore, the customer requested, "We want to reduce the risk of momentary stops and eliminate the trouble of workers rushing to rearrange the bag each time."
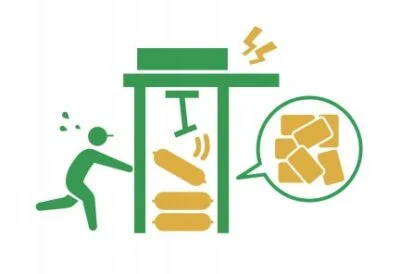
Suggestions from TSUKASA
Utilization of 3D vision cameras and AI
We proposed the "Depalletizer Robo PV" with a 3D vision camera installed on the top of the automatic conveyor machine and AI (artificial intelligence) to analyze the captured images. It processes the captured-image data three-dimensionally. Images are captured in intervals when the automatic conveyor machine is moving, so there is no increase in cycle time.
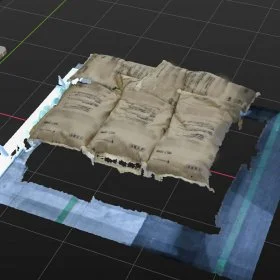
Points of the TSUKASA system
⚫︎Accurate grasp of "wrinkles" and "overlaps"
TSUKASA has accumulated a wealth of experience in handling raw material bags dating back to before the debut of AI. Through careful examination and by letting AI learn, it is possible to detect "wrinkles" and "overlaps" on the surface of the bag with high accuracy, which is generally considered difficult. The optimal picking position is quickly computed.
⚫︎Elaborate testing prior to introduction
When proposing the "Depalletizer Robo PV," TSUKASA receives the powder raw material (raw material bag) that the customer actually uses, it then conducts sufficient verification within TSUKASA, and thoroughly confirms the detection accuracy before considering introduction.
⚫︎ Mechanically advanced picking
The "Depalletizer Robo," which takes instructions from AI to pick up raw material bags, is the fruit of TSUKASA's long-standing technology. We have a wealth of experience in the robot hand's suction pad, and you can discover the effect of 1 + 1 = 3 or more by synergistic effect with PowVision.
TSUKASA has accumulated a wealth of experience in handling raw material bags dating back to before the debut of AI. Through careful examination and by letting AI learn, it is possible to detect "wrinkles" and "overlaps" on the surface of the bag with high accuracy, which is generally considered difficult. The optimal picking position is quickly computed.
⚫︎Elaborate testing prior to introduction
When proposing the "Depalletizer Robo PV," TSUKASA receives the powder raw material (raw material bag) that the customer actually uses, it then conducts sufficient verification within TSUKASA, and thoroughly confirms the detection accuracy before considering introduction.
⚫︎ Mechanically advanced picking
The "Depalletizer Robo," which takes instructions from AI to pick up raw material bags, is the fruit of TSUKASA's long-standing technology. We have a wealth of experience in the robot hand's suction pad, and you can discover the effect of 1 + 1 = 3 or more by synergistic effect with PowVision.
Results of introduction
⚫︎Resolved defective adsorption and improved overload
"The problem of defective adsorption of the bag being less than 0.5% of the total," and "No error in load when pressing the pads" were achieved.We have made great progress toward zero defect rate.
⚫︎ Reduction of human workload
The occurrence of momentary stops is greatly reduced, and there is no need for workers to reload bags.
⚫︎No procedure for registering coordinates or setting instructions
There is no need to set the stowage condition every time at startup, and human work is "just one push of the start button." There is no need to worry about misconfiguration.
"The problem of defective adsorption of the bag being less than 0.5% of the total," and "No error in load when pressing the pads" were achieved.We have made great progress toward zero defect rate.
⚫︎ Reduction of human workload
The occurrence of momentary stops is greatly reduced, and there is no need for workers to reload bags.
⚫︎No procedure for registering coordinates or setting instructions
There is no need to set the stowage condition every time at startup, and human work is "just one push of the start button." There is no need to worry about misconfiguration.
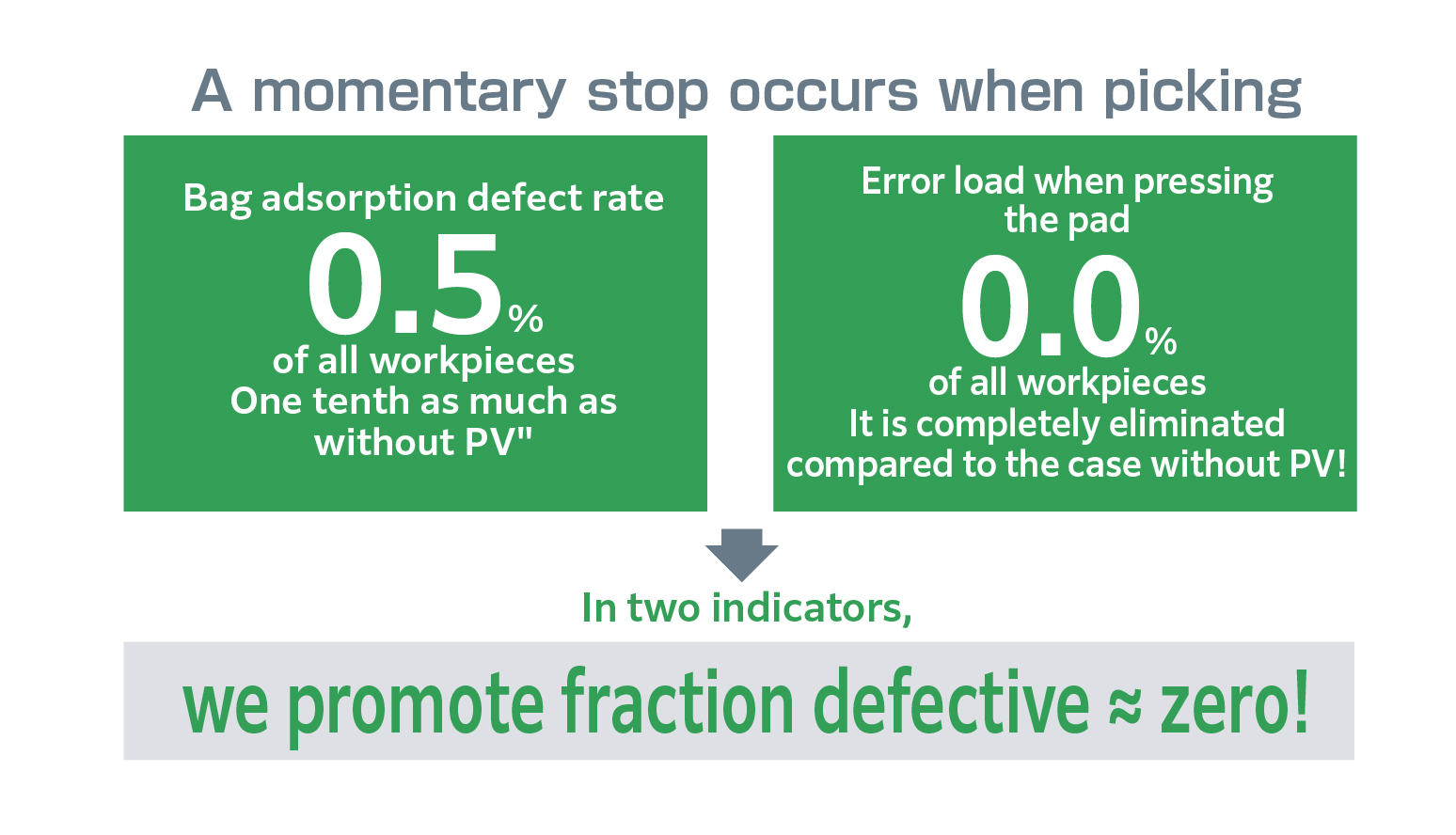
Note: Numerical data on the occurrence of defects will vary depending on the condition of the raw material bag and the stacked condition. Thank you for your understanding.
Recommended for the following customers!
・An automation system was introduced, but the defect rate has not decreased much
・The stowage condition of raw material bags is poor, making it difficult to introduce robots!
・The number of imported raw materials is increasing and there are too many types!
・We want to eliminate the trouble of setting picking coordinates and teaching mistakes!
・The stowage condition of raw material bags is poor, making it difficult to introduce robots!
・The number of imported raw materials is increasing and there are too many types!
・We want to eliminate the trouble of setting picking coordinates and teaching mistakes!
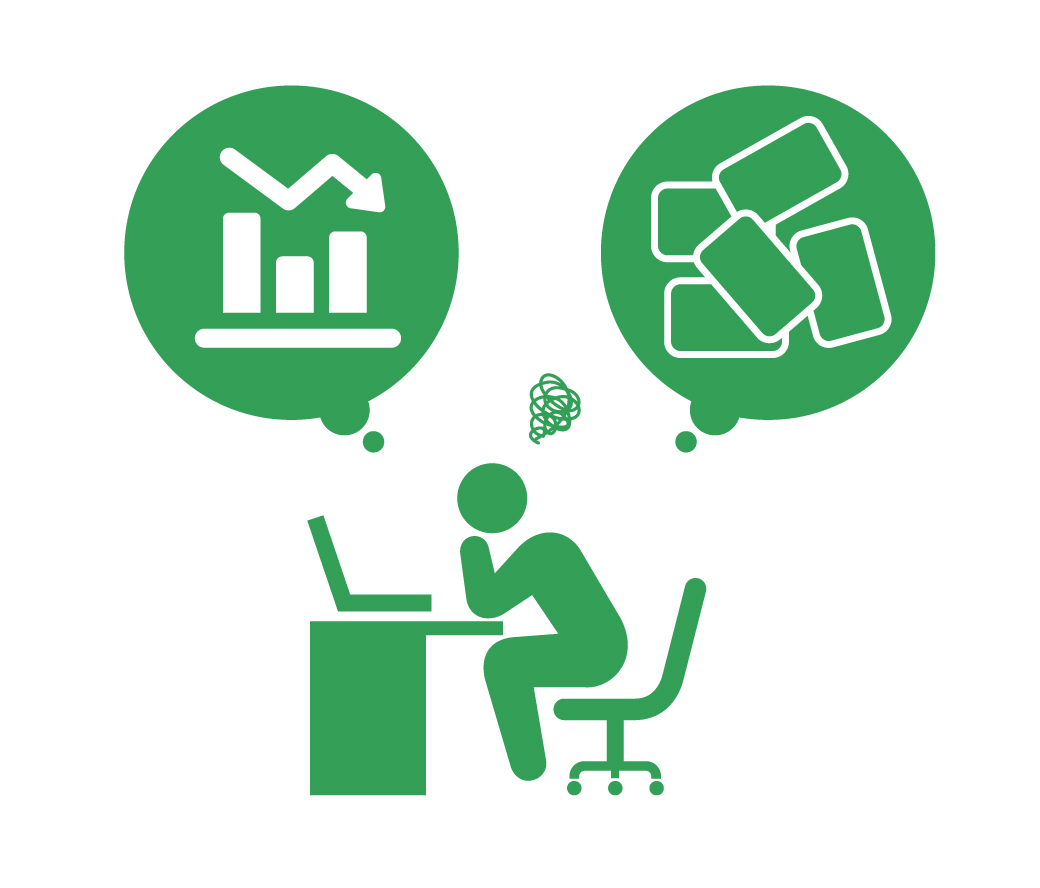