Case Studies
Case Examples
Launch of a new factory utilizing an automated warehouse system
Material Receiving and Powder Feeding Process
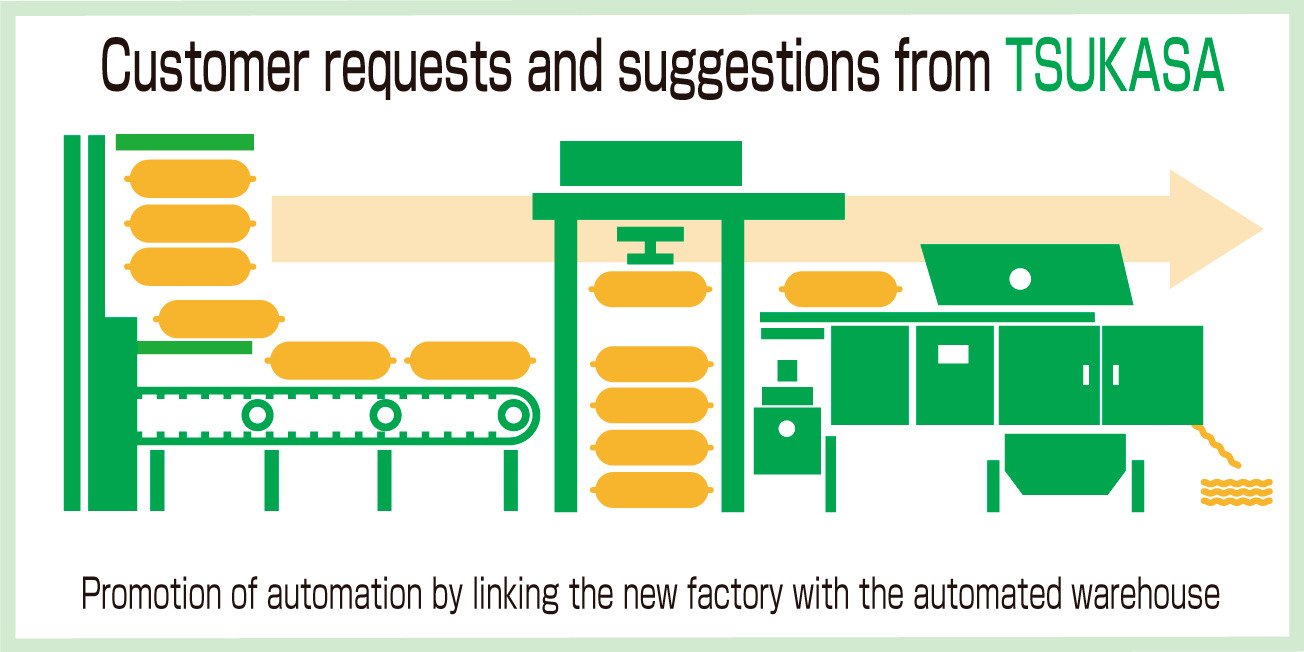
Type of Industry
Bread making company
Introduced Products
Automatic bag opening system + automated warehouse system
Customer requests
Build a highly efficient system from scratch for the new factory
The customer wanted to pursue efficiency in every step of operations in building the new factory. They told us that they wanted to implement labor saving as much as possible, by eliminating bag-opening and feeding work done by people in receiving materials such as flour, and other work like "putting a pallet with a bag of materials on the robot" or "replacing empty pallets after bag supply."
Suggestions from TSUKASA
Proposed to link the automatic bag opening system with the automated warehouse system
⚫︎Automatic bag opening system
This system is unique to TSUKASA, combining functions of supplying material bags with robots, automatically opening bags and taking out materials, and removing foreign objects in a single unit.
⚫︎In conjunction with the automated warehouse system
Since the automatic bag system automatically transports pallets exactly when the "next material bag" is needed, it eliminates the need for manual pallet loading and pallet replacement.
See details of the product
This system is unique to TSUKASA, combining functions of supplying material bags with robots, automatically opening bags and taking out materials, and removing foreign objects in a single unit.
⚫︎In conjunction with the automated warehouse system
Since the automatic bag system automatically transports pallets exactly when the "next material bag" is needed, it eliminates the need for manual pallet loading and pallet replacement.
See details of the product
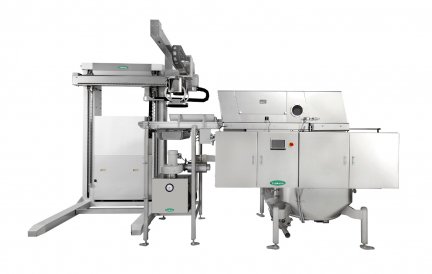
Results of introduction
People only "monitor" and process empty bags
⚫︎People only "monitor" and process empty bags
With the automatic bag opening and automated warehouse linking, people only have to monitor if the pallet being transported is correct and to process the empty bags. It has eliminated the effort to lift and open material bags, contributing significantly to labor saving.
⚫︎Eliminated material feeding errors
Even with the use of many materials, optimal flow, zoning, computer controlled picking, and shipping instructions within automated warehouses have helped eliminate human errors and prevent any feeding errors.
⚫︎Effective use of space for factories and warehouses
The use of a streamlined, efficient, and cutting-edge automated warehouse system has allowed material stocks to be organized without wasted space, making effective use of the entire factory space.
With the automatic bag opening and automated warehouse linking, people only have to monitor if the pallet being transported is correct and to process the empty bags. It has eliminated the effort to lift and open material bags, contributing significantly to labor saving.
⚫︎Eliminated material feeding errors
Even with the use of many materials, optimal flow, zoning, computer controlled picking, and shipping instructions within automated warehouses have helped eliminate human errors and prevent any feeding errors.
⚫︎Effective use of space for factories and warehouses
The use of a streamlined, efficient, and cutting-edge automated warehouse system has allowed material stocks to be organized without wasted space, making effective use of the entire factory space.
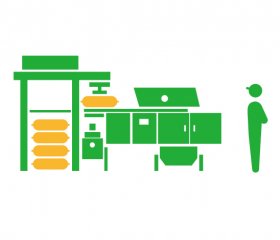