Case Studies
Useful Worksite Knowledge
Preventive Maintenance, Predictive Maintenance, and Breakdown Maintenance
Maintenance of facilities and machinery is essential to maintain a stable production capacity. In this page, we will introduce three types of maintenance styles: "Preventive maintenance," "predictive maintenance," and "breakdown maintenance."
What are the differences between the three types of maintenance styles?
Preventive maintenance: Maintenance work performed regularly to prevent failures

Preventive maintenance: Maintenance work performed regularly to prevent failures

Breakdown maintenance: Maintenance work performed in response to failures, production capacity reductions, occurrence of defective products, etc.

Advantages and disadvantages of each maintenance
Advantages of preventive maintenance
Improvement of production quality: Production quality is guaranteed since parts are replaced before a failure occurs.
Improvement of productivity and reduction of property damage: The occurrence of defective products is also reduced, resulting in the improvement of productivity and reduction of damages.
Improvement of productivity and reduction of property damage: The occurrence of defective products is also reduced, resulting in the improvement of productivity and reduction of damages.
Disadvantages of preventive maintenance
Increase in work hours: It requires more labor and costs due to the increase in work hours for regular replacement of parts, etc.
Benefits of predictive maintenance
Reduction of unnecessary maintenance work: Unnecessary and non-urgent work can be reduced, such as the elimination of regular replacement of "still usable parts."
Disadvantages of predictive maintenance
Requires installation of sensors: It requires the cost of installing sensors at various locations along the line to detect signs of failures.
Advantages of breakdown maintenance
Normally does not require resources for maintenance: There is no need to allocate personnel or costs to maintenance work until failures, etc. occur.
Requires low costs if it is minor property damage: In some cases, you can manage with minimal action depending on the situation of failures, etc.
Requires low costs if it is minor property damage: In some cases, you can manage with minimal action depending on the situation of failures, etc.
Disadvantages of breakdown maintenance
Increase in risk to production activities: If a problem suddenly occurs, it may lead disruptions in production plans, such as line stoppages.
May take some time to recover: It may take a long time to determine the cause of failure, manufacture the parts and replace them."
May take some time to recover: It may take a long time to determine the cause of failure, manufacture the parts and replace them."
TSUKASA's approach towards maintenance work
Together with our customers, we will think about the best mix of preventive and predictive maintenance in addition to the conventional breakdown maintenance.
For example
PowOpener (automatic bag-opening equipment) is equipped with a "predictive maintenance" function as standard.
● Driving motor
Counts operation hours and displays the total operation hours on the panel
● Cylinder
Counts the number of drives and displays the total number on the panel
The upper limit time and the number of drives can be set as desired according to the operating conditions of the line. An alarm will notify you when the maintenance period is approaching.
Counts operation hours and displays the total operation hours on the panel
● Cylinder
Counts the number of drives and displays the total number on the panel
The upper limit time and the number of drives can be set as desired according to the operating conditions of the line. An alarm will notify you when the maintenance period is approaching.
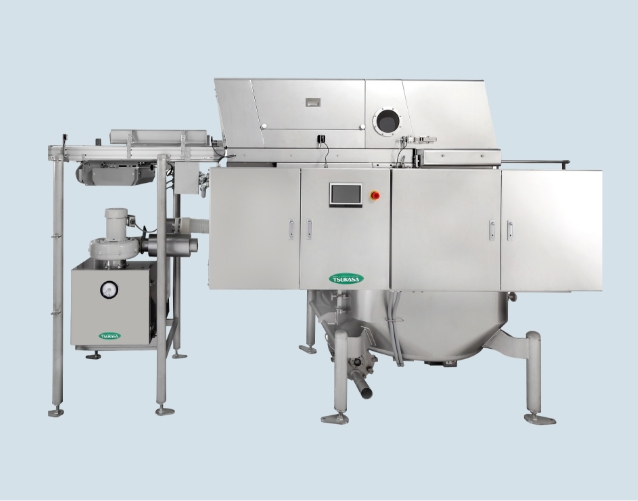