Case Studies
Useful Worksite Knowledge
Plant layout
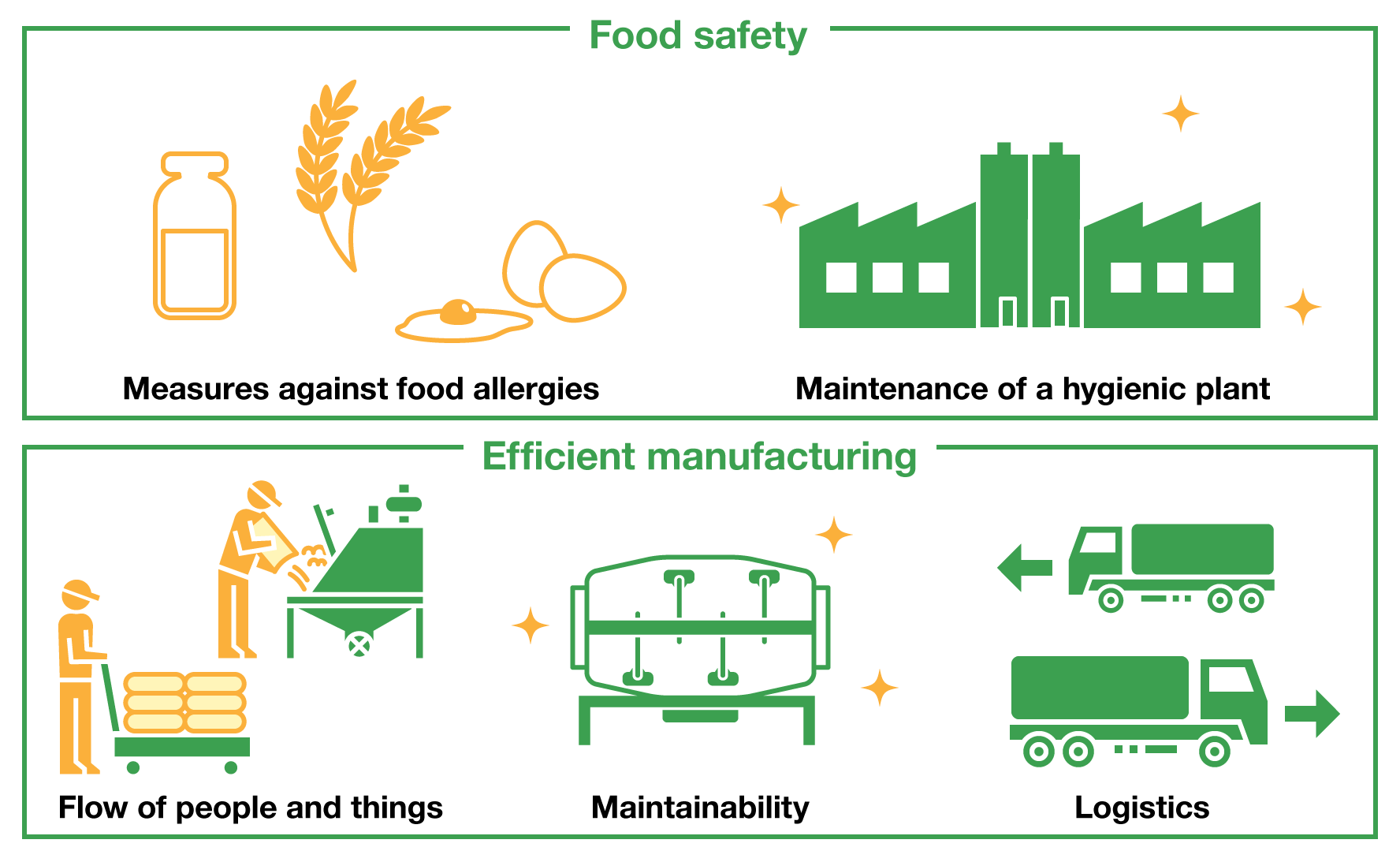
At a plant which manufactures food such as confectionery and bread produced from powder, there are many processes starting from receiving raw material powder (wheat flour etc.,) to shipping out finished products. The plant is divided into two areas: One is the polluted area (where powder swirls around) and the other is the product area (where final processes such as baking and molding are performed).
When designing the plant layout, two points should be met concerning ideal facility design for both areas―"Food safety" and "Efficient manufacturing."
When designing the plant layout, two points should be met concerning ideal facility design for both areas―"Food safety" and "Efficient manufacturing."
Things to pay attention to for food safety
Measures against food allergies
At a plant which manufactures products containing allergens, the polluted area where dust particles swirl around, and the product area need to be clearly divided in the plant layout. In addition, in order to avoid accidents where allergens turn to particles and get contaminated with other processes, the polluted area where powder often swirls around is separated for each product, and equipment is installed in the area such as dust collectors which suppress swirling dust particles.
Maintenance of a hygienic plant
In order to maintain food hygiene, it is important to not only conduct periodic maintenance and cleaning for facilities and machines, but also prevent particles which adhere to people from getting contaminated with other things. When designing the plant layout, take into consideration the ease of maintenance of machines and the traffic of people coming in and out of the plant, and make it possible to always maintain a hygienic environment.
For performing efficient and stable manufacturing
Flow of people and things
In order to manufacture products while reducing waste as much as possible, it is necessary to properly consider and design the flow of raw materials being delivered to the plant, the location of staff and facilities, and the completion of products.
Shorten the distance of people's movements to reduce unnecessary actions. In addition, if the distance between various processes is shortened, the distance for conveying raw materials and materials can also be reduced. By making an efficient plant layout which reduces a significant amount of waste while clearly partitioning the polluted area and product area can also enhance safety.
Shorten the distance of people's movements to reduce unnecessary actions. In addition, if the distance between various processes is shortened, the distance for conveying raw materials and materials can also be reduced. By making an efficient plant layout which reduces a significant amount of waste while clearly partitioning the polluted area and product area can also enhance safety.
Maintainability
It is necessary to periodically clean facilities and machines, etc., and remove any remaining raw materials, dirt, and dust to maintain cleanliness. In order to perform cleaning efficiently, it is important to secure the space around the facilities and machines, and create a layout that enables easy cleaning. In maintaining a clean plant, it is possible to lower the occurrence of defective products and maintain a high level of product safety.
Logistics
Raw material reception and shipment of manufactured products are conducted by trucks and cars. In many cases the locations for vehicles entering and leaving are close together, so designing a plant layout by considering where vehicles come in and go out of will improve efficiency.
The number of defects, product safety, and manufacturing efficiency will change significantly depending on the plant layout.
TSUKASA has a large lineup of products which can provide a high level safety and design an efficient plant layout. Furthermore, we can offer the ideal plant layout with the knowledge founded on our long years of experience.
Feel free to contact us.
TSUKASA has a large lineup of products which can provide a high level safety and design an efficient plant layout. Furthermore, we can offer the ideal plant layout with the knowledge founded on our long years of experience.
Feel free to contact us.