Case Studies
Useful Worksite Knowledge
Equipment design for worker safety during cleaning
The top causes of occupational accidents that occur in food manufacturers are "falls," "getting caught / entangled," and "cuts/abrasions." This is thought to be because efficiency and productivity are so important that the necessary procedures for cleaning are often omitted.
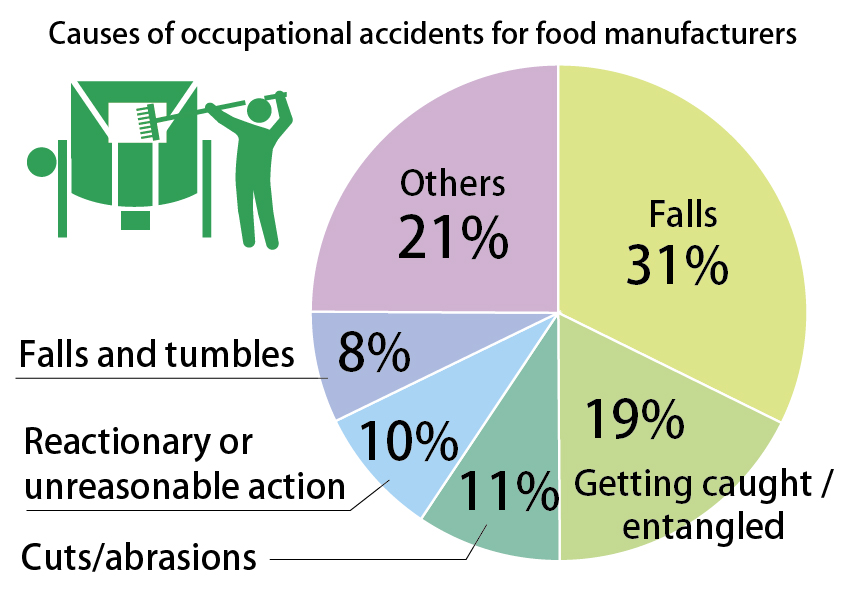
Has the following ever happened?
We want to start cleaning as soon as possible
Before the rotating object comes to a complete stop, workers open the door and try to stop it with their hands.
We don't want to turn it off
During cleaning without turning off the power, other unaware worker operates the equipment.
Reinstallation of safety grid is troublesome
Operation started without reinstallation of safety grid after cleaning. Someday, somebody might put their hands into the equipment.
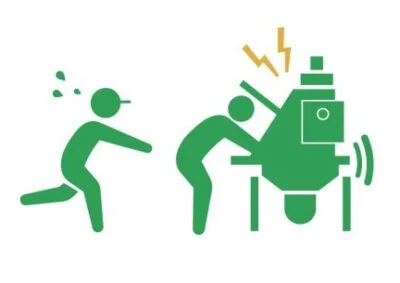
To prevent dangerous omission actions
TSUKASA safety design examples
⚫︎Lock-type safety switch
The door will not open until the sensor detects the complete stop of the rotating object.
⚫︎Proximity switch on inspection gate
The equipment does not operate when the door for cleaning is open (no sensor detection).
⚫︎ Proximity switch on safety grid
The equipment does not operate when there is no safety grid (no sensor detection).
⚫︎ Protective fence + Laser curtain
The perimeter of the equipment is surrounded by protective fences, and laser curtains are installed at the entrance to detect people walking in and out of the area. If there is an unforeseen intrusion, the line stops immediately.
The door will not open until the sensor detects the complete stop of the rotating object.
⚫︎Proximity switch on inspection gate
The equipment does not operate when the door for cleaning is open (no sensor detection).
⚫︎ Proximity switch on safety grid
The equipment does not operate when there is no safety grid (no sensor detection).
⚫︎ Protective fence + Laser curtain
The perimeter of the equipment is surrounded by protective fences, and laser curtains are installed at the entrance to detect people walking in and out of the area. If there is an unforeseen intrusion, the line stops immediately.
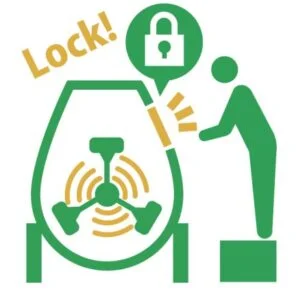
Mandatory acts performed by the customer
Be sure to turn off the equipment before cleaning. In addition, put a sign such as "Cleaning in progress" on the operation panel, and keep the operation key of each equipment at the hands of the cleaner.
For example, in Line Mill® (mill)
Lock-type safety switch is adopted on the door. The equipment can only be operated when the door is locked. In addition, even after the stop operation, the rotating disk rotates by inertia for a certain period of time, but the lock is set so that the rotating disk cannot be accessed until it comes to a complete stop.
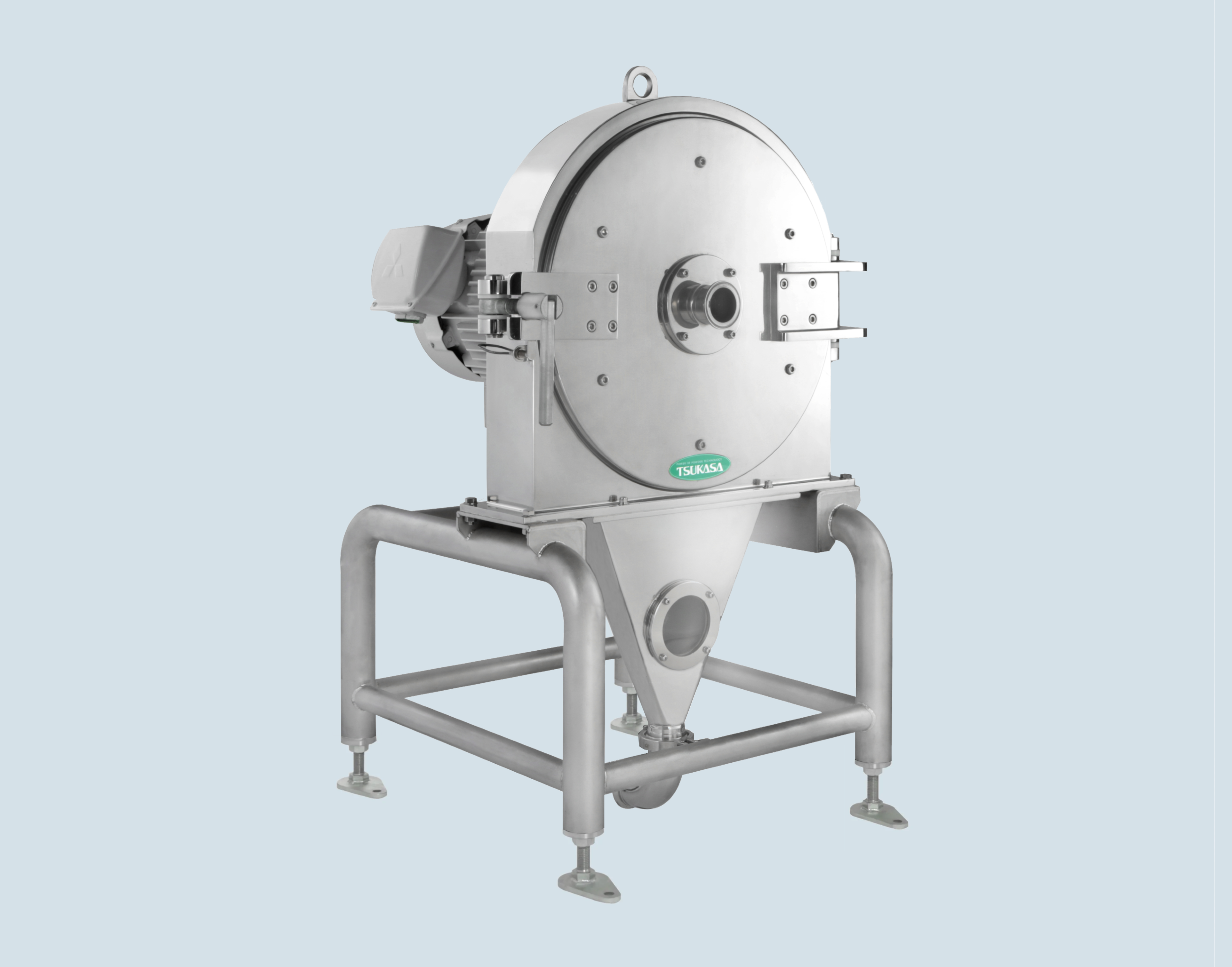
TSUKASA's commitment to safety
⚫︎Compliance with customer safety standards
After the safety standards set by your plant is provided to us, we will propose equipment design and plant layout in a form that complies with the standards.
⚫︎ Tailor-made support
For example, we can add a cover to the drive part of the equipment and meet the customer's request for further safety measures.
⚫︎ Implementation of operation training
At the time of delivery of the equipment, we will hold a workshop at the customer's plant and carefully explain matters such as "when to press the emergency stop switch."
After the safety standards set by your plant is provided to us, we will propose equipment design and plant layout in a form that complies with the standards.
⚫︎ Tailor-made support
For example, we can add a cover to the drive part of the equipment and meet the customer's request for further safety measures.
⚫︎ Implementation of operation training
At the time of delivery of the equipment, we will hold a workshop at the customer's plant and carefully explain matters such as "when to press the emergency stop switch."
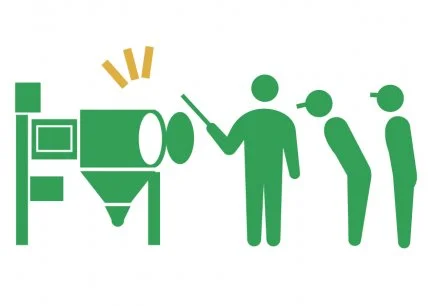