Case Studies
事例集&豆知識
事例集
副原料の高精度計量“40h”が“8h”に短縮!
計量工程
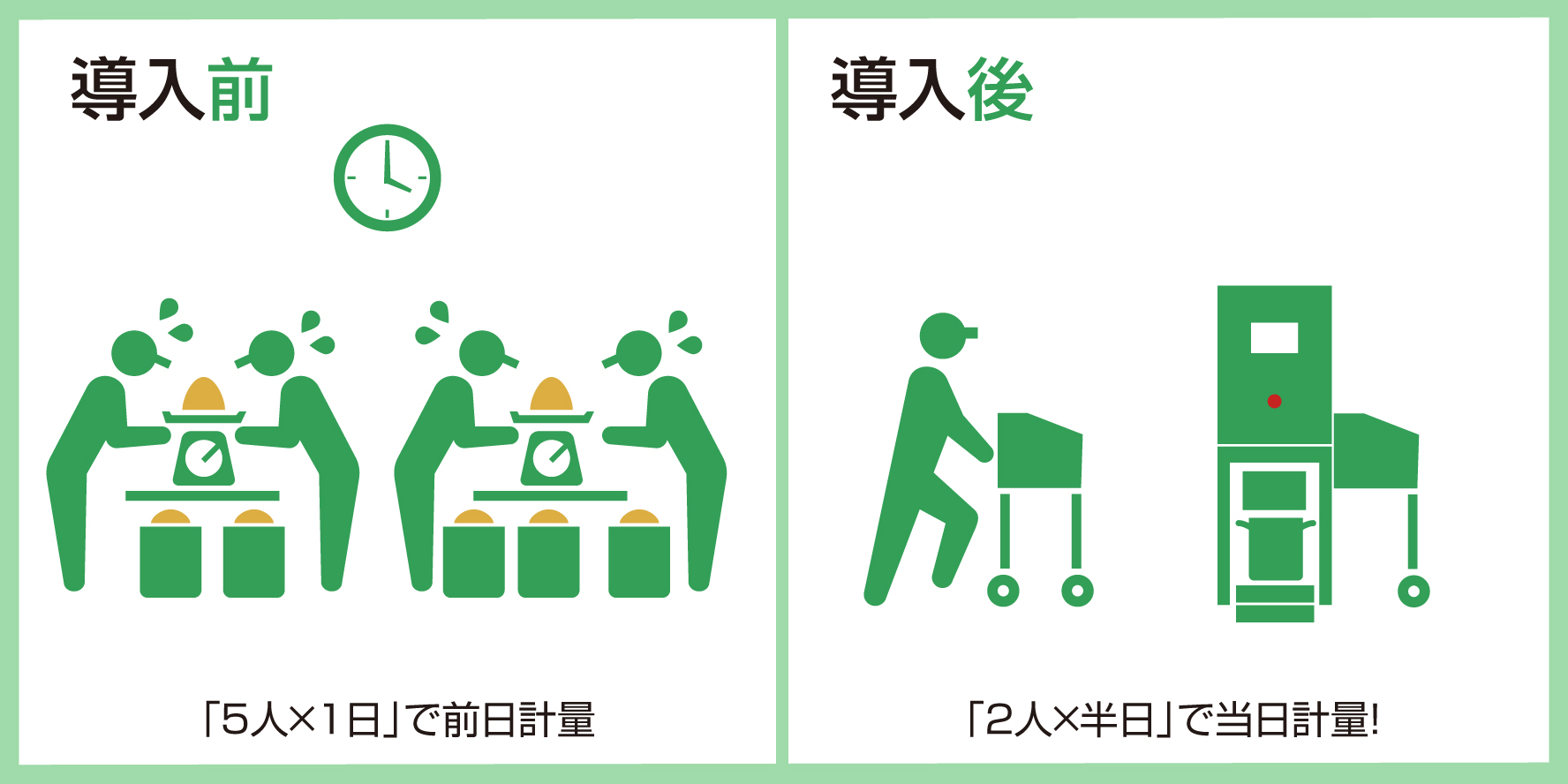
業種
製菓会社様
導入製品
ディバイダースケール・ターミナル着脱型
背景と課題
多品種少量に対応した計量作業の負担増
ある製菓工場では米粉やモチ粉など主原料は自動計量していましたが、グラニュー糖や乳酸菌など副原料は手計量でした。「種類の多い副原料は小まわりのきく手作業で」とのお考えでしたが、多品種少量生産の進行とともに計量作業に求められる厳密さが増し、ついには“専従5人がかりで丸1日”を要するまでに。近年の人手不足もあって他工程から作業者をまわすことも難しく大きな懸念材料でした。
◎人手による高精度計量の課題
●作業量に比例して人員が必要
●作業者の習熟が必要
●微量の誤差調整に手間
●粉塵飛散に細心の注意
●作業者の習熟が必要
●微量の誤差調整に手間
●粉塵飛散に細心の注意
TSUKASAからのご提案
ストッカ着脱型の計量機で大幅な効率化
最大4カ所で原料ストッカが着脱使用できて、添加原料を入れ替えて配合できる「ディバイダースケール・ターミナル 着脱型」をご提案しました。ストッカは8台を用意してローテーションで使用できるシステムとしました。
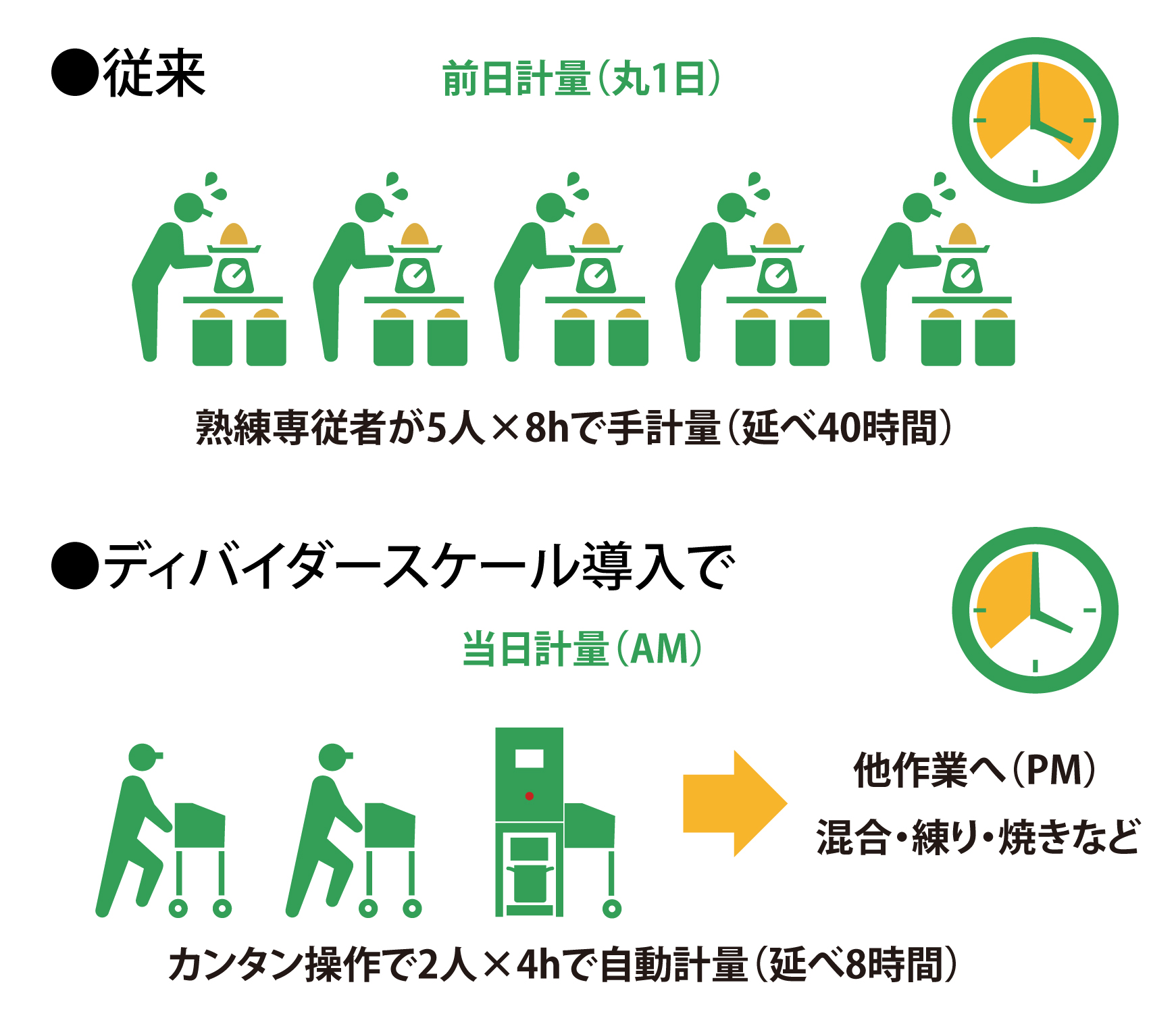
前日計量
“5人×8時間”で丸1日(延べ40時間)が
↓
当日計量
“2人×4時間”で(延べ8時間)に短縮!
“5人×8時間”で丸1日(延べ40時間)が
↓
当日計量
“2人×4時間”で(延べ8時間)に短縮!
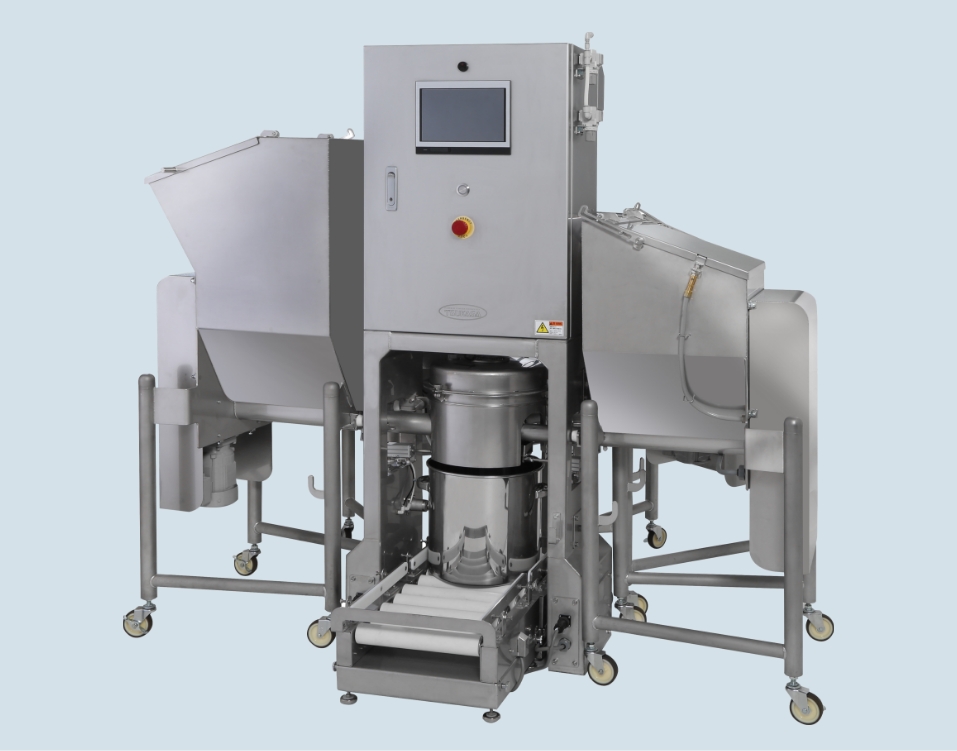
ディバイダースケール・ターミナル着脱型
導入の効果
人員配置に大きなゆとり
大幅な効率化で計量作業にかかる人員が少なくなり、その分を他工程にまわすことが可能に。人手不足で「管理職まで生産ラインに入って」というケースがなくなりました。
計量ミスや“選び間違い”の解消
自動計量なのでヒューマンエラーの心配はなし。見た目のよく似た原料を作業者が選び間違えて計量するミスもなくなりました。
人員募集や定着率にも貢献
作業者の負担軽減は「すぐに人がやめてしまう」というお悩み解消にも貢献。また作業環境への配慮は新規採用でも強みになると期待できます。
省力化に貢献するとともに経済的
同じ容器で複数の原料を配合計量して、そのまま次工程へ持ち込み投入が可能です。また1原料ごとに袋に計り入れる必要がなくなり、使用する袋の削減にもなって経済的です。