Case Studies
事例集&豆知識
事例集
自動計量を高効率&省スペースで実現
計量工程
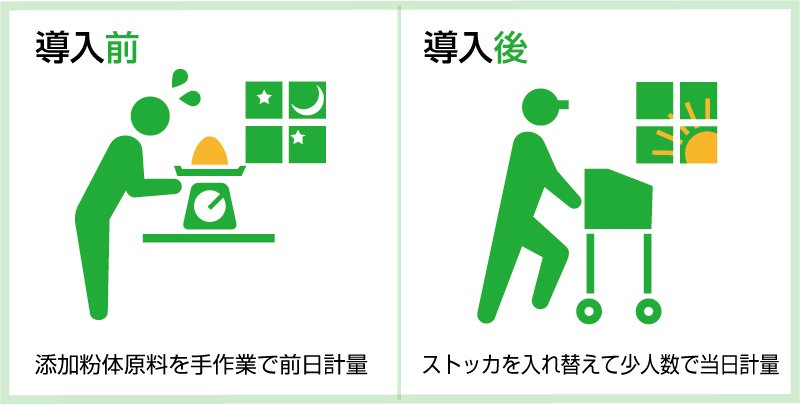
業種
水産加工食品メーカー様
導入製品
ディバイダースケール・ターミナル 着脱型
背景と課題
多くの人手をかけての前日計量を何とか効率化したい
水産加工食品の製造で、調味料など添加粉体原料を10種類以上使用していました。翌日に使う分の計量は専任スタッフ5人の手作業で行っており、1日がかりの労力が必要でした。人手不足の影響もあって自動化を検討しましたが、工場内には大きな機械を置くスペースがありません。そこで「何とかならないか?」とご相談をいただきました。
TSUKASAからのご提案
ストッカ着脱型の計量機なら省スペースで自動化が可能
最大4か所で原料ストッカが着脱できて、添加原料を入れ替えて配合できる「ディバイダースケール・ターミナル 着脱型」をご提案しました。ディバイダースケール2台に対してストッカは10台を用意し、さらに効率よくローテーションできるよう配慮しました。
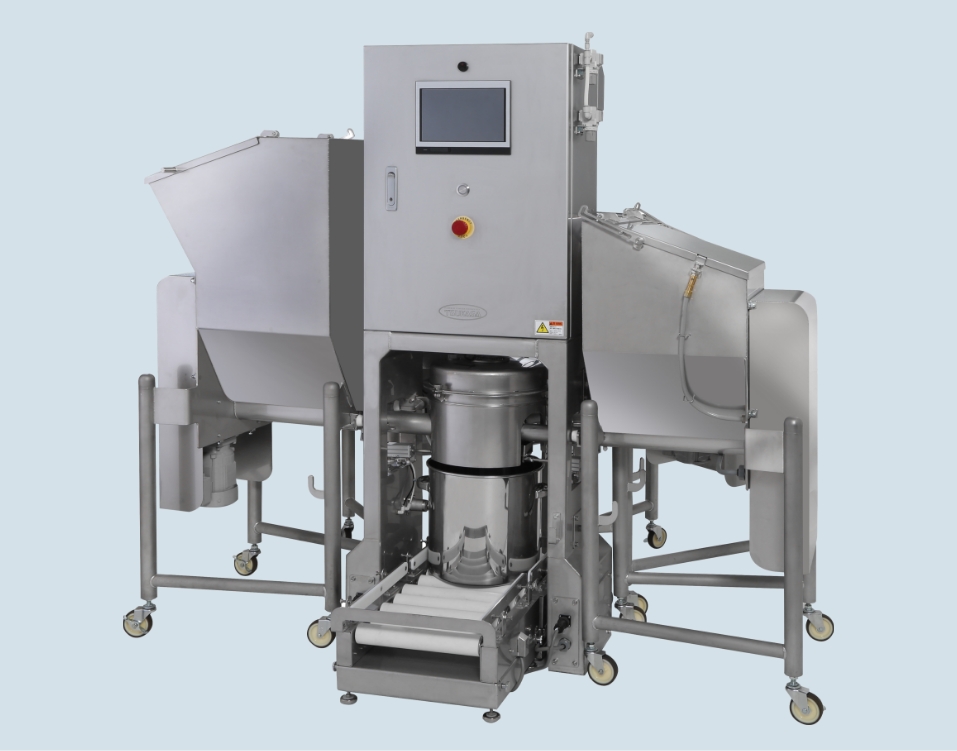
TSUKASAが選ばれた理由
⚫︎コンベア不要で工場空間を有効利用
複数のストッカが着脱可能な自動小分け計量機はTSUKASAオリジナル仕様。何台も計量機を並べてコンベアで容器を搬送する必要がないため、工場の省スペース化にも大きく貢献できます。
複数のストッカが着脱可能な自動小分け計量機はTSUKASAオリジナル仕様。何台も計量機を並べてコンベアで容器を搬送する必要がないため、工場の省スペース化にも大きく貢献できます。
⚫︎画像認識による誤投入防止も可能
添加原料の取り違えを防ぐため、画像認識システムの搭載も可能です。原料袋のラベルをカメラで撮影して「この投入口にはこの原料を」と一致した場合のみストッカのロックが解除される仕組みです。
添加原料の取り違えを防ぐため、画像認識システムの搭載も可能です。原料袋のラベルをカメラで撮影して「この投入口にはこの原料を」と一致した場合のみストッカのロックが解除される仕組みです。
⚫︎導入前に入念な試験運転
お客様から原料をお借りして社内で試験を行い、さらにお客様の工場でもテストを繰り返して「どれくらい効率化できるか」を実証していきました。
お客様から原料をお借りして社内で試験を行い、さらにお客様の工場でもテストを繰り返して「どれくらい効率化できるか」を実証していきました。
導入の効果
⚫︎「5人×1日」が「2人×半日」の作業に
朝一番に2人で計量をスタートすれば、その日の混合機の最初の稼働にも十分間に合うように。当日分の計量は午前中に終わって午後には別の作業ができるため、人手不足が緩和されて毎日の仕事に余裕が生まれました。
朝一番に2人で計量をスタートすれば、その日の混合機の最初の稼働にも十分間に合うように。当日分の計量は午前中に終わって午後には別の作業ができるため、人手不足が緩和されて毎日の仕事に余裕が生まれました。
⚫︎食品トレーサビリティも向上
「何日の何時何分にどの原料を何kg計量したか」の履歴が保存されるため、トラブル発生の際には時系列をさかのぼっての追跡ができるようになりました。
「何日の何時何分にどの原料を何kg計量したか」の履歴が保存されるため、トラブル発生の際には時系列をさかのぼっての追跡ができるようになりました。
⚫︎投入前の再チェックが不要に
従来はストッカへの投入前に原料の種類を再チェックしていました。画像認識システムの導入により、この手間もなくすことができました。
従来はストッカへの投入前に原料の種類を再チェックしていました。画像認識システムの導入により、この手間もなくすことができました。
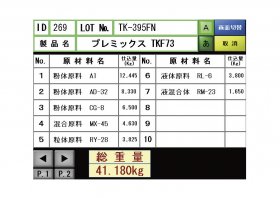