Case Studies
事例集&豆知識
現場で役立つ豆知識
予防保全・予知保全・事後保全
安定した生産能力の維持には設備・機械などの保全業務が欠かせません。今回は「予防保全」「予知保全」「事後保全」という3種類の保全スタイルをご紹介します。
3種類の保全スタイルの違いとは?
予防保全:故障を起こさないため定期的に行う保全業務

予知保全:故障の兆候を事前に発見して行う保全業務

事後保全:故障・生産能力低下・不良品発生などに対応して行う保全業務

各保全のメリット・デメリット
予防保全のメリット
生産品質の向上:故障発生前に部品交換などを行うため生産品質が保証されます。
生産性の向上・物損の削減:不良品の発生も削減されて生産性が向上し、物的損害の発生も抑制できます。
生産性の向上・物損の削減:不良品の発生も削減されて生産性が向上し、物的損害の発生も抑制できます。
予防保全のデメリット
作業工数の増大:定期的な部品交換などで作業工数が増えるため労力とコストがかかります。
予知保全のメリット
不要な保全業務を削減:“まだ使える部品”の定期交換がなくなるなど不要不急の作業が削減できます。
予知保全のデメリット
センサーの設置が必要:故障の兆候を検知するセンサーをライン各所に設置するコストがかかります。
事後保全のメリット
普段は保全へのリソースが不要:故障などが発生するまでは保全業務に人やコストをあてる負担がありません。
軽微な物損ならコストが少額:故障などの状況にあわせて最小限の対応ですませる場合もあります。
軽微な物損ならコストが少額:故障などの状況にあわせて最小限の対応ですませる場合もあります。
事後保全のデメリット
生産活動へのリスクが増大:突発的なトラブルが発生すれば、ライン停止など生産計画に混乱が生じる可能性もあります。
復旧に時間を要することも:故障原因の究明→部品製作→取り替えまでに長期間を要する恐れもあります。
復旧に時間を要することも:故障原因の究明→部品製作→取り替えまでに長期間を要する恐れもあります。
保全業務に対するツカサの取り組み
従来の事後保全に加えて予防保全・予知保全とのベストミックスをお客様とともに発想します。
例えば
パウオープナー(自動開袋機)では「予知保全」機能を標準搭載
●駆動モーター
稼働時間をカウントして合計稼働時間をパネル表示
●シリンダー
駆動回数をカウントして合計駆動回数をパネル表示
ラインの稼働状況などにあわせて上限時間や回数を自在に設定可能。保全時期が近づくとアラームで告知します。
稼働時間をカウントして合計稼働時間をパネル表示
●シリンダー
駆動回数をカウントして合計駆動回数をパネル表示
ラインの稼働状況などにあわせて上限時間や回数を自在に設定可能。保全時期が近づくとアラームで告知します。
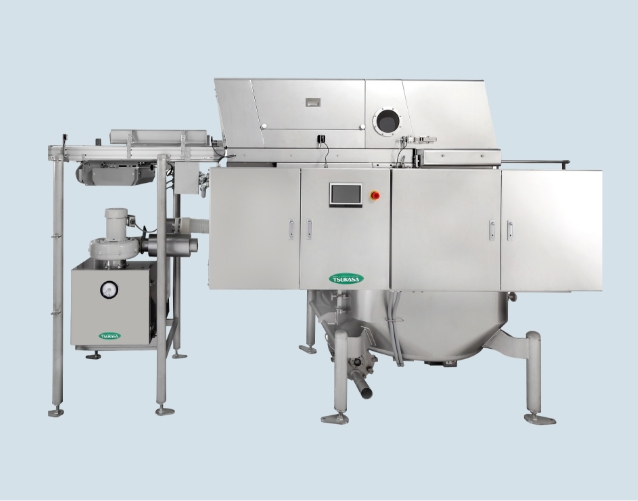